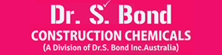
Care Of Material : It Is Absolutely Necessary That Ironyte Be Kept Until It Is Used.
Cement : Shall Be Equal In All Respect. To Indian Standard Specification. Ordinary Portland cement is be preferred to rapid hardening.
Aggregate : Shall be clean, crushed granite1/4 in. and down (kapchi).
Water : Shall be clean & fresh.
Mix 1 part of ironyte with 4 parts of cement in the dry state.
To one part of this mixture. Add two parts of clean, sharp granite chips, ¼ in.
Mix again thoroughly and add just the necessary quantity of clean fresh water, to make a thick slurry.
Where it is more desirable to have a dustless floor, rather than great resistance to heavy trucking, a smaller proportion of ironyte need be used in the first mix, i.e. one part of ironyte to 5 parts of cement. Then proceed as in the case of heavy – duty floors.
Quantities : The following ready reckoner gives the quantities of ironyte required for different types of floor, and for varying thickness, at a glance.
Thickness of topping | Duty | Ironyte required per 100 sq. mtrs of floors |
½" (12/13 mm) | Heavy | 250 Kgs Approx. (Say 5 Bags) |
½" (12/13 mm) | Light | 190 Kgs Approx. (Say 4 Bags) |
¾" (18/19 mm) | Heavy | 350 Kgs Approx. (Say 7 Bags) |
¾" (18/19 mm) | Light | 280 Kgs Approx. (Say 5.2 Bags) |
As soon as the underlying has been leveled up to within ½" of the finishing surface the ironyte topping is run in whilst the under laying surface is still wet. When the initial set takes place the surface is trowelled to smooth finish with a steel trowel. In projects where the floor can be completed in one operation the granolithic layer can be dispensed with by bringing the base up to within ½''- ¾" of the finishing level and the following on with the ironyte topping, whilst the base is still wet.
First remove the old concrete surface to a depth of at least 2". clear away all loose particles and dust thoroughly. Soak the surface for at least 12 hours. To prevent the absorption of mixing water into a dry base. Immediately prior to laying the topping, any surplus water should be mopped up, and a neat cement grout thoroughly worked in the surface. Now. While the cement grout is still wet, ordinary granolithic to develop the thickness of ½'' - ¾'' of ironyte topping when the initial set takes place, trowel a smooth finish with a steel trowel.
Alternatively, lay on ironyte topping 2" thick in one operation. N.B.: the fact that the proper preparation of the base to take a topping often receives breakage of edges and segregation but perfunctory attention is undoubtedly responsible for a great trouble. E.g. lifting and cracking.
Dry cement, or mixture of dry cement and sand should not be sprinkled directly on the surface with the object of absorbing moisture of stiffening the mix. The final trowelling should not be begun until pressure with the fingers ceases to make any indentation
Keep the ironyte topping damp, with wet sacks or sand, for 10 days before submitting the floor for trucking. The mixing of ironyte with cement should always be very thorough to an even colour, whilst in a dry state.
The topping must always be laid as a separate and final operation. The laying of Ironyte topping whilst not, being a specialist 's job, does required to be done by a man accustomed to finishing ordinary granolithic with steel trowel. Ironyte does not retard the setting time of cement.
Test made by ironyte, floor toppings suffer only one- third loss in surface wear, and loss in weight in comparison with good ordinary concrete finished floors.
Ironyte does not chip off from top surface of the floor.
Ironyte does not rust.
Provides a high strength impact & abrasion resistance wearing surface
Gives up to 8 times the abrasion resistance of plain cured concrete.
Free of rust, oil, and non – ferrous materials.
Dense surface resists penetration of oil, grease and many other liquids.
Virtually non- dusting in service.
Easy to clean.
Floors subjected to acids or other corrosive chemicals
(1) By Hand (2) By Shovel
May be applied at rates 2.5 to 11 kgs/m2 depending on the degree of protection required.
25 kgs. HDPE bags with polyethylene liners for moisture protection. Precautions and limitations
1. do not use air- concrete.
2. do not use concrete containing calcium chloride based admixtures.
3. Proper curing and sealing is required.
The following direction should be carefully followed while applying Ironyte floor hardener.
These directions are to be followed for application of ironyte floor hardener on well. Designed, non air- entertained concrete mixes at temperatures of between 160 to 450c.
Sub- grade and reinforcing: special attention should be given to a well – compacted and level sub- grade.A sub grade that is not well compacted could cause cracking in the slab. Follow the specification for use of reinforcing bars.
Do not use calcium chloride or calcium chloride base admixture in the concrete.
The finished floor must be cured and sealed immediately after finishing to prevent oxidation of the surface.
Keep air in the concrete below3%
Do not use air – entrained admixture.
Check the specification for the amount of hardener required per square meter, then stack the correct number of bags at each by to be placed that day. This is important because it gives the finishers a " gauge" for applying the correct amount of material.
After the above conditions have been met proceed with work in the following manner:
Place concrete between screed points and strike off to level of finished floor.
Use bull float to level the surface. Allow the slab to bleed. To removed bleed water, drag surface with burlap or rubber hose.
After the concrete has stiffened to the point of supporting floating operations, open the surface by hand floating or power floating. Normally, a finisher's footprint of 6.4 mm to 9.5mm depth indicates that a slab is ready for power floating. Earlier floating of the slab edges by hand is strongly recommended since edges will dry first.
For best result and uniformity of thickness, ironyte should be applied in two shakes using approximately tow – thirds of the total amount for the first pass and remaining one third to be broadcasted in the second pass .
Immediately after the slab surface has been opened by floating, apply the first shake in a uniform application by had, spreader or any other suitable method.
Allow the first shake to remain un worked on the surface until it has absorbed moisture and achieved a dark uniform color. Then float with hand or power float. Immediately apply second shake starting from the edges.
After second shake has absorbed its moisture, float in the same manner as outlined above, working the edges first, then cross floating for a level, uniform surface.
First steel trowelling.: when the surface, has set sufficiently so that no additional water or fines are brought to the surface, a second and final trowelling shall be given to the floor. During this operation the trowel should be slightly raised to give a hard and smooth finish. The trowelling process should
Cure the surface with water ponding for 8 days.